2014 Chevrolet Silverado 1500 Detailed Finite Element Model
Version 3a, released Download Silverado zip 72.8 MB →
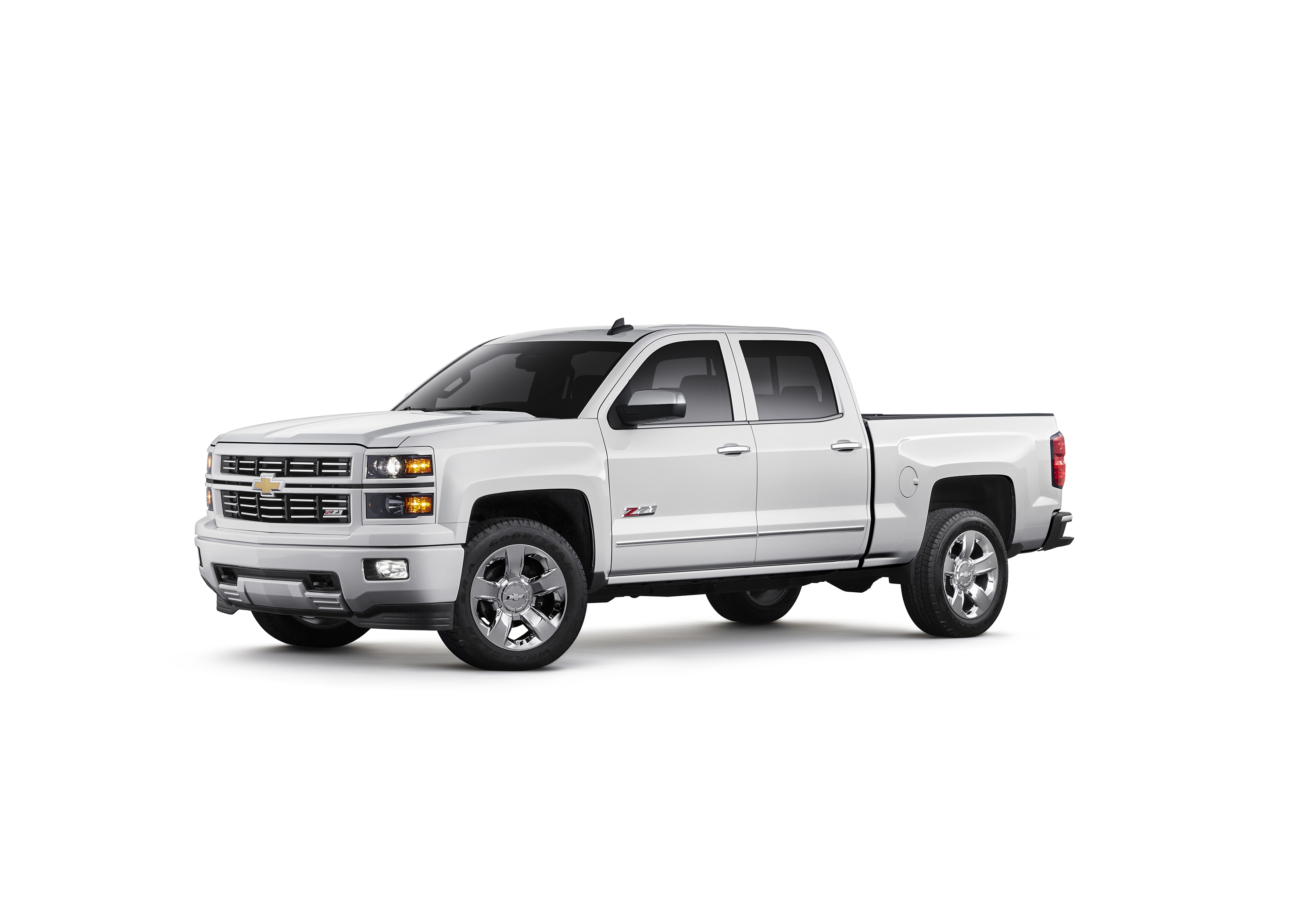
Vehicle Description
VIN | 3GCUKPEC7 |
---|---|
Body Type | 4-Door crew cab short box pick-up truck |
Weight | 2,367 kg (5,218 lb) |
Engine Type | 5.3L V8 Ecotec3 |
Transmission | 6L80 Hydra-Matic 6 speed Automatic |
Tire Size | P255/70R17 |
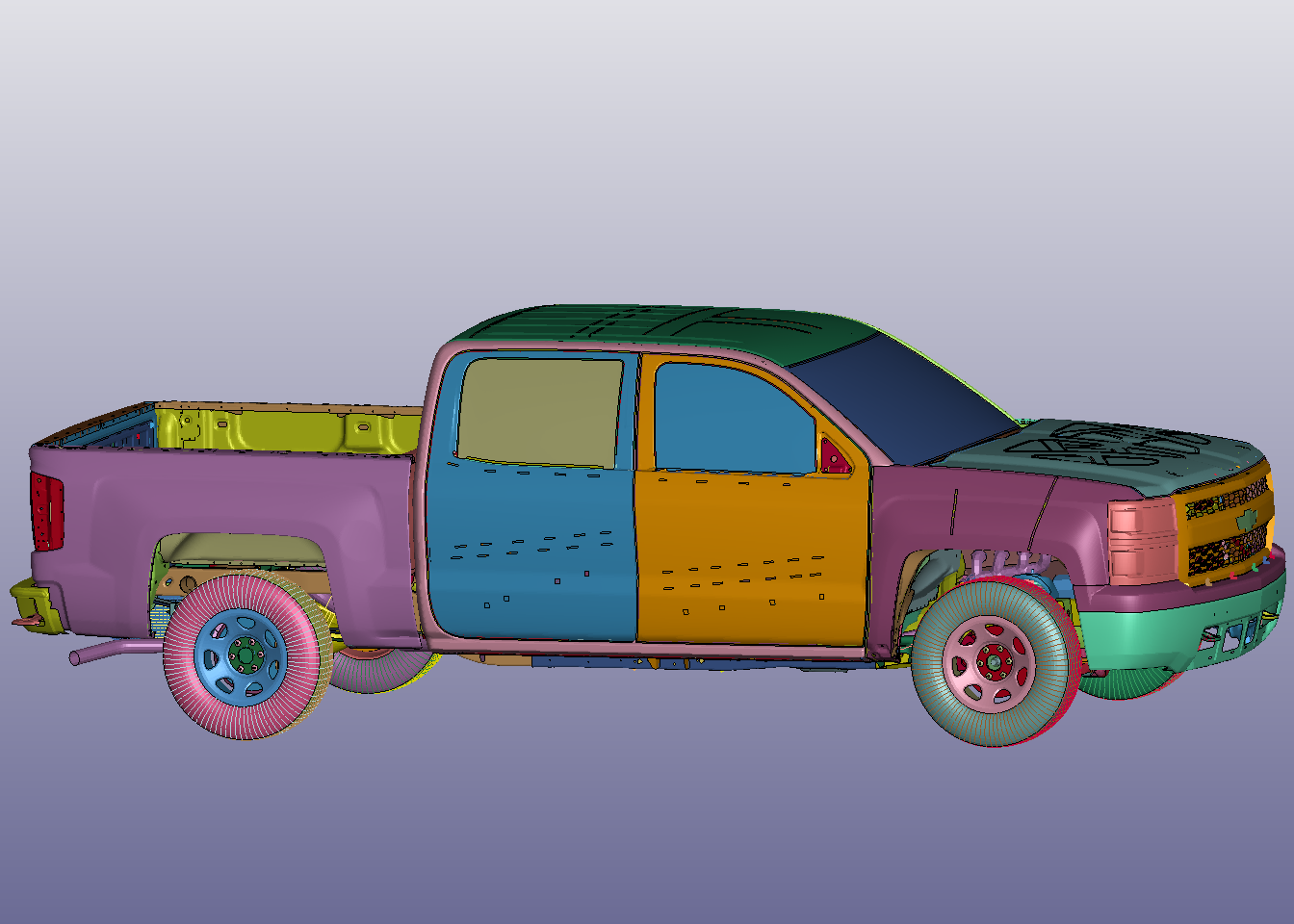
Version 3 Model Details
Elements | 2,960,781 |
---|---|
Nodes | 2,809,811 |
Parts | 1,501 |
Features | Structural components details, Suspension system details, Uniform mesh throughout (to support multi mode impacts) |
References
- 2014 Chevrolet Silverado 1500 Finite Element Detailed Mesh Model Validation, Presentation | doi:10.13021/f4yf-yd73
This model is the computer representation of a 2014 Chevrolet Silverado pick-up truck for use in crash simulations. The model was developed through reverse engineering by EDAG Inc. under a contract with the National Highway Traffic Safety Administration. The model was updated by CCSA to make it in a similar setup as other models posted on the CCSA website. EDAG performed a comprehensive vehicle tear down for engineering analysis that included manufacturing technology assessment, material utilization and complete vehicle geometry scanning. The geometry and material test data from the baseline vehicle tear down was used to build detailed finite element analysis (FEA) simulation models suitable for crashworthiness using LS-DYNA.
The model was validated against several full-scale crash tests. It is expected to support current and future research related to occupant risk and vehicle compatibility, as well as roadside barrier crash evaluation, research, and development efforts.
Initial verification and validation of the model included completeness checks, comparisons of actual and model inertial properties, and comparisons to actual full-scale crash test data.
The resulting detailed finite element vehicle model has about 3 million elements. It includes details of the structural and drivetrain components. The model was constructed to include full functional capabilities of the suspension and steering subsystems allowing for non-level terrain analyses.
Average element size of the model is 6–8 mm with a minimum size of 4 mm. Typical simulation time step is 0.5 µs. The model was created for use with the LS-DYNA nonlinear explicit finite element code. Approximate computation time to run a 100 ms simulation using 16 cores is hours.
Related stories and links
- “Mass Reduction for Light-Duty Vehicles for Model Years 2017-2025,” Final Report, NHTSA DTNH22-13-C-00329.
- “Structural Countermeasure/Research Program: Mass and Cost Increase Due to Oblique Offset Moving Deformable Barrier Impact Test,” NHTSA Report No. DOT HS 812 523, April 2018.
2014 Chevrolet Silverado 1500 Coarse Finite Element Model
Version 3a, released Download Silverado zip 25.5 MB →
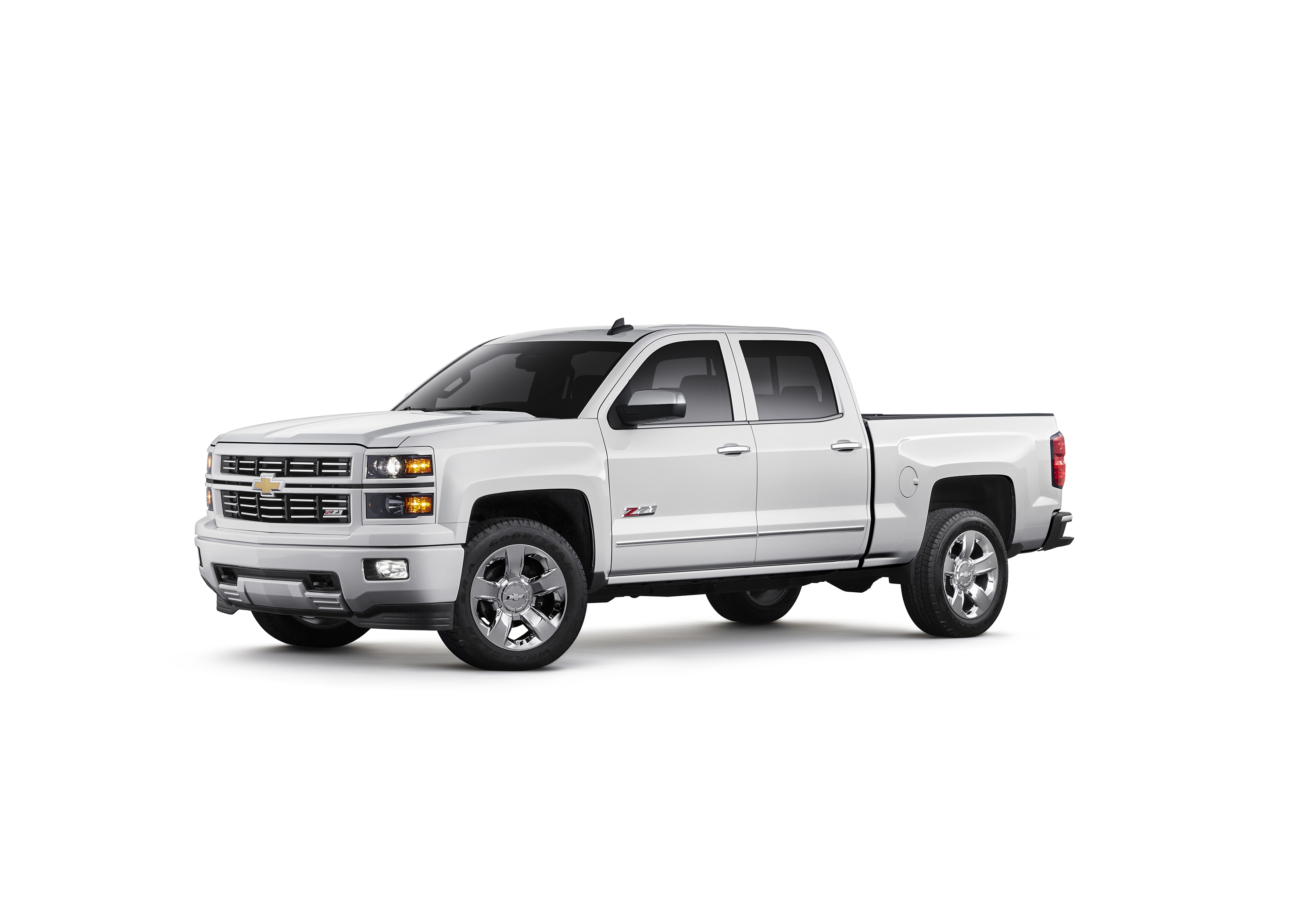
Vehicle Description
VIN | 3GCUKPEC7 |
---|---|
Body Type | 4-Door crew cab short box pick-up truck |
Weight | 2,367 kg (5,218 lb) |
Engine Type | 5.3L V8 Ecotec3 |
Transmission | 6L80 Hydra-Matic 6 speed Automatic |
Tire Size | P255/70R17 |
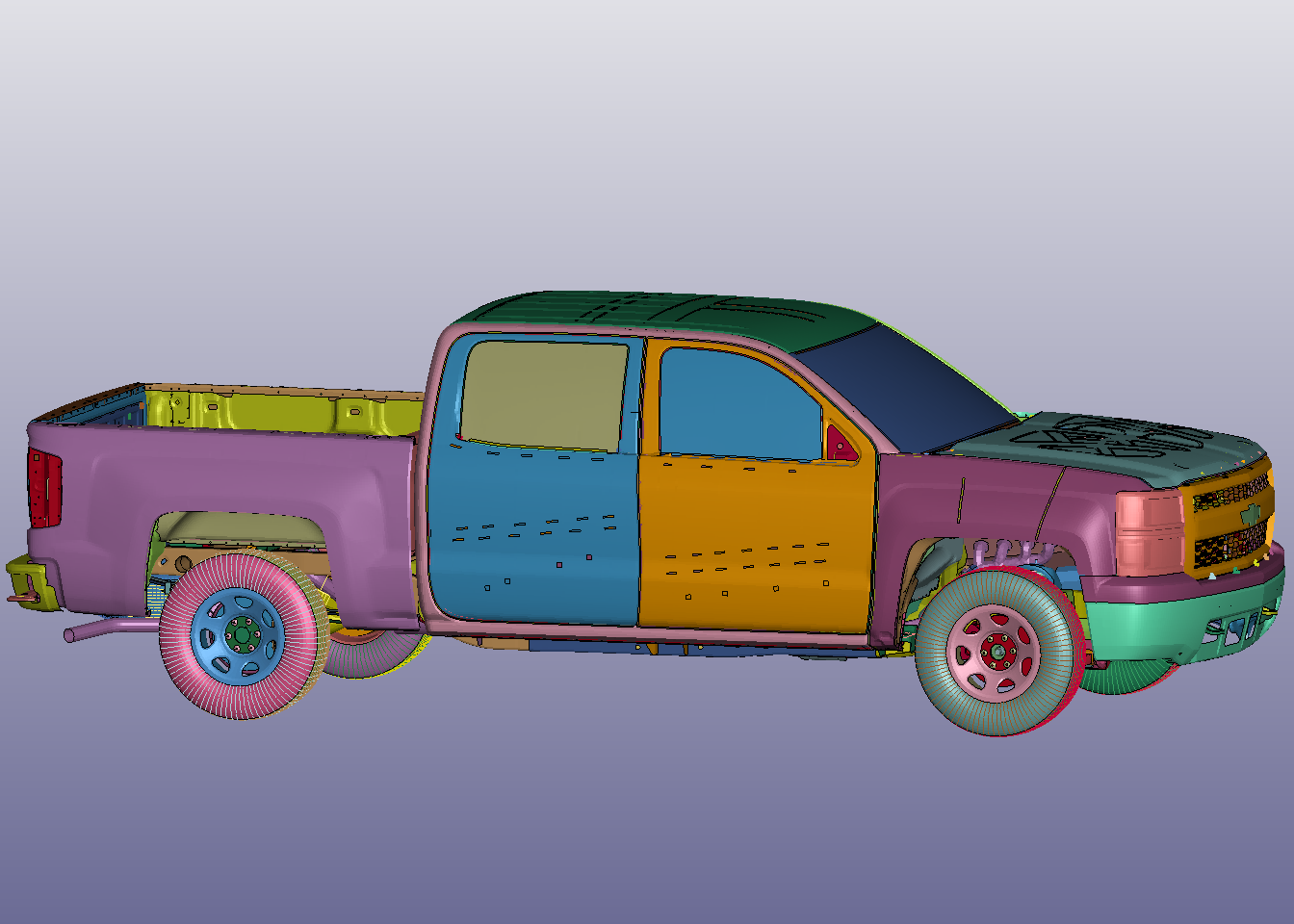
Version 3 Model Details
Elements | 1,099,961 |
---|---|
Nodes | 958,855 |
Parts | 1,503 |
Features | Structural components details, Suspension system details, Uniform mesh throughout (to support multi mode impacts) |
References
- 2014 Chevrolet Silverado 1500 Finite Element Coarse Mesh Model Validation, Presentation | doi:10.13021/p6mn-hp79
This model is the computer representation of a 2014 Chevrolet Silverado pick-up truck for use in crash simulations. It was developed based on the detailed mesh finite element vehicle model of the 2014 Chevrolet Silverado pick-up truck model. The detailed mesh model was developed by EDAG Inc. The coarse mesh version of the model was created by the Center for Collision Safety and Analysis researchers under a contract with the Federal Highway Administration.
The model was validated against a full-scale rigid wall crash test. It is expected to support current and future research related to occupant risk and vehicle compatibility, as well as barrier crash evaluation, research, and development efforts.
Initial verification and validation of the model included completeness checks, comparisons of actual and model inertial properties, suspension response tests, and comparisons to actual frontal crash test data. Subsequent efforts will compare simulation results to other available crash tests.
The resulting coarse finite element vehicle model has about 1.1 million elements. It includes details of the structural and drivetrain components. The model was constructed to include full functional capabilities of the suspension and steering subsystems allowing for non-level terrain analyses.
Average element size of the model is 15–25 mm with a minimum size of 6 mm. Typical simulation time step is 1.0 µs. The model was created for use with the LS-DYNA nonlinear explicit finite element code. Approximate computation time to run a 100 ms simulation using 16 cores is .
Related stories and links
- “Mass Reduction for Light-Duty Vehicles for Model Years 2017-2025,” Final Report, NHTSA DTNH22-13-C-00329.
- “Structural Countermeasure/Research Program: Mass and Cost Increase Due to Oblique Offset Moving Deformable Barrier Impact Test,” NHTSA Report No. DOT HS 812 523, April 2018.
→ SHA512-256(2014-chevy-silverado-detailed-v3a.zip)= 53113c250fe7c9835ef6b82f8380a1f6b2d4a07963404e60b8c41a8571585ad7
→ SHA512-256(2014-chevy-silverado-coarse-v3a.zip)= 260bc55d25a4d0101470fa538f3852afcb6bd057637b839c885ec229c59b3f07